Our Services
Materials That Can Be Coated
The proposed solid lubricants are versatile and suitable for application on various metallic surfaces, including steel in its different forms (high-speed steel, stainless steel, carbon steel, etc.), aluminum and titanium alloys, copper, brass, and more. Moreover, they can be effectively used on carbide, ceramic, and plastic surfaces as well. Table 1 outlines essential traits of these recommended coatings.
Materials | Coating Composition | Thickness (μm) | COF |
---|---|---|---|
SS / HSS/ CS/ Al / Ti | WS2 | 0.05 – 0.1 | 0.01 – 0.1 |
SS / HSS/ CS/ Al / Ti | WS2/Various form of carbon | 1.5 – 3.0 | 0.1 – 0.2 |
SS / HSS/ CS/ Al / Ti | WS2/ MoS2 | 1.0 – 1.5 | 0.05 – 0.15 |
SS / HSS/ CS/ Al / Ti | WS2/ Teflon | 1.0 – 3.0 | 0.1 – 0.15 |
Application of the Coating
Various methods are employed to apply the coating to customer parts, including pressurized gas spraying (using air, nitrogen, argon, etc.), brushing, and sputtering. Customers have the option to choose whether the coatings are deposited at an ambient temperature, with or without binders or adhesives, based on their requirements.
Our approach ensures excellent adhesion of the coating to the customer parts, achieving thicknesses ranging from 0.5 μm to 3.0 μm. We also offer surface modification and hardening of parts, tailored to customer preferences, which further enhances the properties and performance of the components.
Prior to the deposition of solid lubricants, several surface modification techniques can be applied, such as anodizing, plating, PVD or CVD coating, nitrating, or other forms of surface enhancements. Each application is meticulously examined on a case-by-case basis, allowing us to select the most suitable and effective coating for the specific requirements of our valued customers.
Benefits and Capabilities of Our WS2 based Coatings
The recommended solid lubricants offer extensive applicability, suitable for use on a wide range of metallic surfaces, including various forms of steel (high-speed steel, stainless steel, carbon steel, etc.), as well as aluminum, titanium alloys, copper, brass, and more. Furthermore, these lubricants can be effectively applied to carbide, ceramic, and plastic surfaces.
For a detailed overview of the suggested coatings, please refer to the table below, which outlines their fundamental characteristics.
Materials | Coating Composition | Thickness (μm) | COF |
---|---|---|---|
SS / HSS/ CS/ Al / Ti | WS2 | 0.05 – 0.1 | 0.01 – 0.1 |
SS / HSS/ CS/ Al / Ti | WS2/Various form of carbon | 1.5 – 3.0 | 0.1 – 0.2 |
SS / HSS/ CS/ Al / Ti | WS2/ MoS2 | 1.0 – 1.5 | 0.05 – 0.15 |
SS / HSS/ CS/ Al / Ti | WS2/ Teflon | 1.0 – 3.0 | 0.1 – 0.15 |
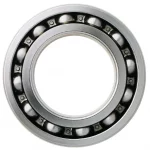
Low Friction Coatings
Genio coatings offer exceptional solutions for safeguarding various sliding, rotating, and reciprocating parts. Whether it’s titanium and steel fasteners, aluminum slides, ball bearings, door locks, or a wide array of other moving and sliding metallic components, these coatings provide excellent protection.
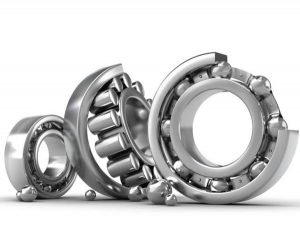
Chrome Steel Ball Bearings
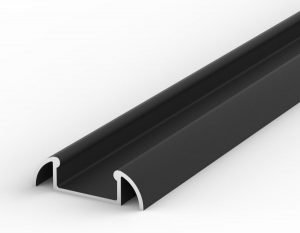
Aluminum Slides
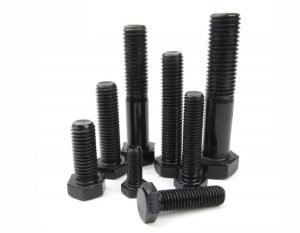
Titanium Flanged Bolt
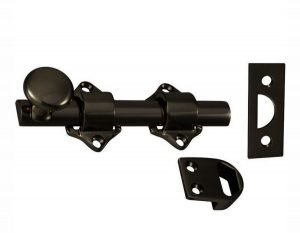
Brass surface door bolt
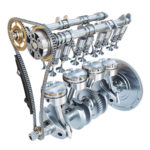
Heat Resistant, Soil Resistant Coatings
Engine Piston Skirts
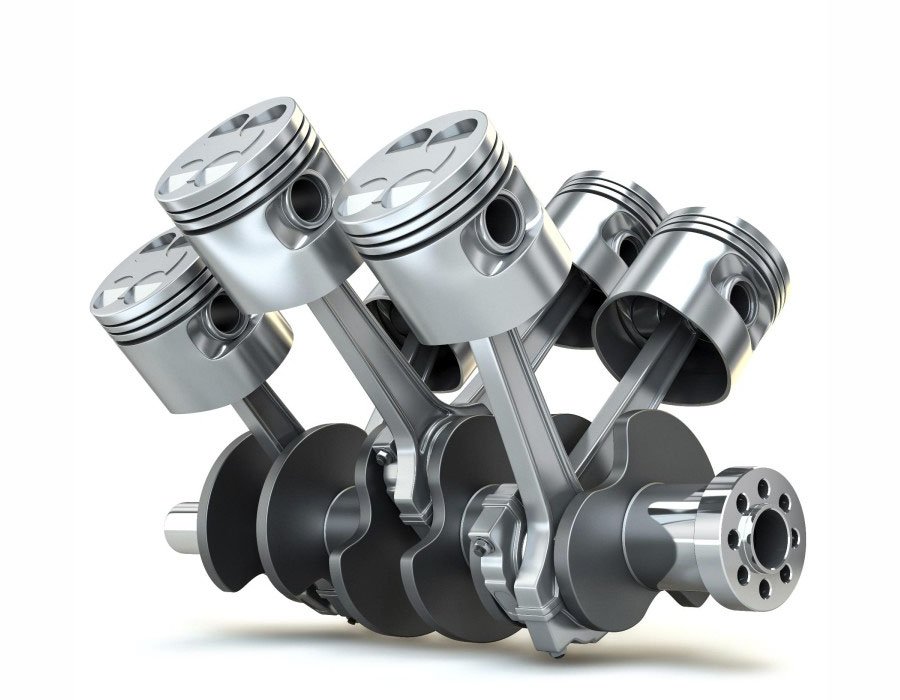
Internal combustion is excellent application for coating that combines: heat restance, antiwear, antifriction and carbon builtup prevention properties. Genio has developed special WS2 / carbon composite coating to extend life of piston at normal operation as well as first and cold start conditions.
Exhaust pipes
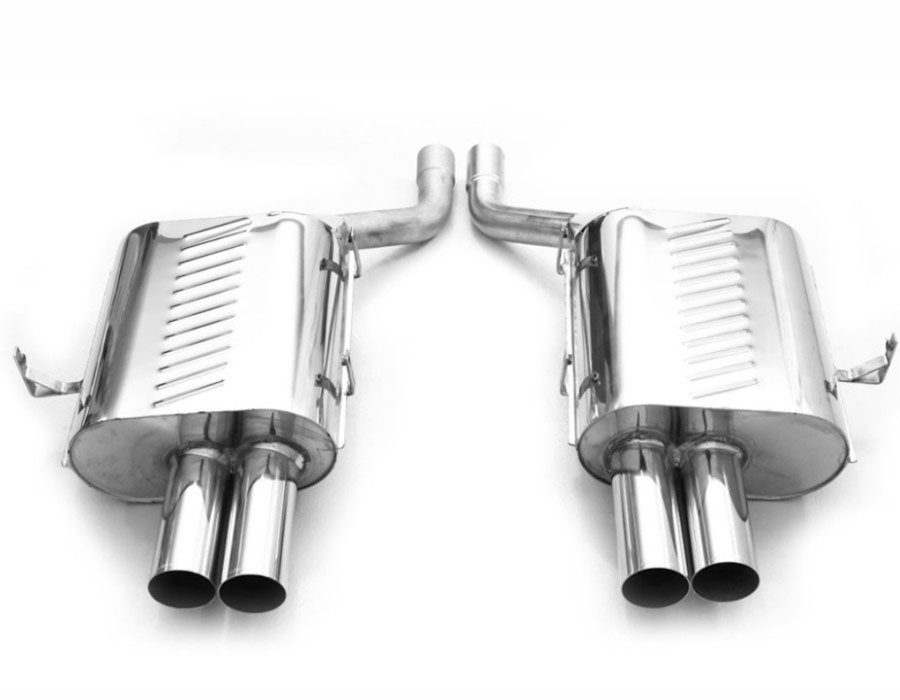
Some of our WS2 / carbon composite coatings could serve as heat-resistant, soil resistant protective layers by preventing carbides, sulphides, and other materials in exhaust gasses from adhering to cast iron, ductile cast iron or aluminium.
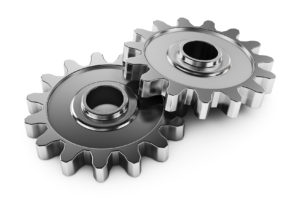
Wear Resistant Coatings
The Genio coating delivers outstanding anti-wear protection, making it a superior choice for numerous heavy-duty and abrasive applications. It excels in safeguarding the threads of CNC machines, forming dies, pinches, carbide end mills, drill bits, and various gear types. In fact, this coating has the potential to extend the lifespan of performing tools by up to 10 times or even more in many cases.
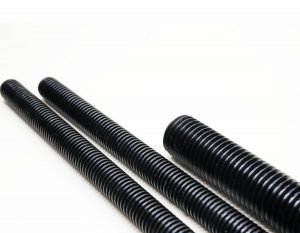
Stainless steel threads
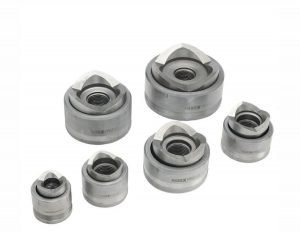
Stainless Steel Die and punch
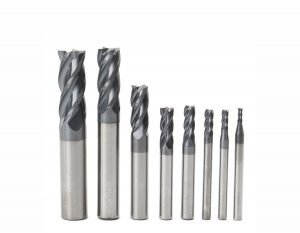
Carbide End Mills and High speed Steel drill bit
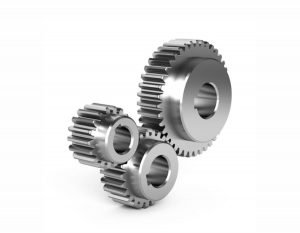